Adaptive Multilayer Model Predictive Control for Hydraulic Systems
Leonardo Cecchin, Robert Bosch GmbH
Hydraulic systems are integral to our modern society, powering a wide range of applications, from industrial machinery to construction equipment. Their efficiency is vital in conserving energy resources.
To address this, the project centers on the creation of an Adaptive Multilayer Model Predictive Controller (MPC) for Hydraulic systems. It entails modeling of the system, the exploration of diverse control strategies across system components, and the holistic assessment of the controller’s architecture. The controller’s performance is rigorously tested through simulation, benchmarked against alternative approaches, and ultimately validated in real-world experimental settings.
Variable Speed Variable Displacement Hydraulic Pump Control
The first part of the project consisted in the study of a real-time non-linear MPC formulation for the control of the Variable-Speed Variable-Displacement hydraulic pump. This also included the development of a novel approach for the evaluation of Look-Up Tables within the optimization problem.
The non-linear MPC formulation has been compared with the industrial state of the art controller, first in a simulation environment, and then on a test-bench. The MPC controller showed improved performances with respect to the state of the art, while allowing a greater flexibility in the face of changes in the components.
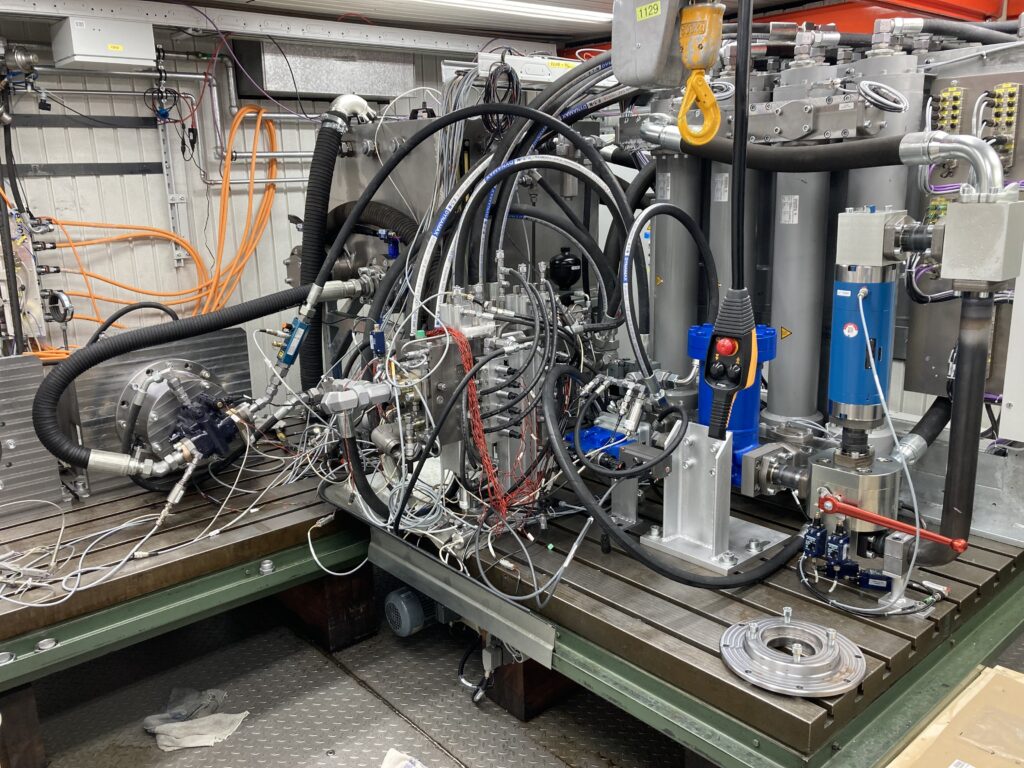
Local Linear Models-based Model Predictive Control for Excavator Digging Assistance Functions
A common application of hydraulic systems is in off-highway construction vehicles, such as excavators. A common and effective way to reduce energy wastage is through advanced excavator digging assistance functions, that help the operator performing repetitive tasks quickly and precisely. This results in less errors, less repetitions, and therefore reduced energy consumption.
A model of the excavator is obtained via Local Linear Models (LLMs), starting from a simple dataset recorded on the machine to be controlled. Using the LLMs a path-tracking MPC is developed, that exploits the linearity of the models for faster computation times. The approach again is tested on a real-world prototype machine, with promising results.
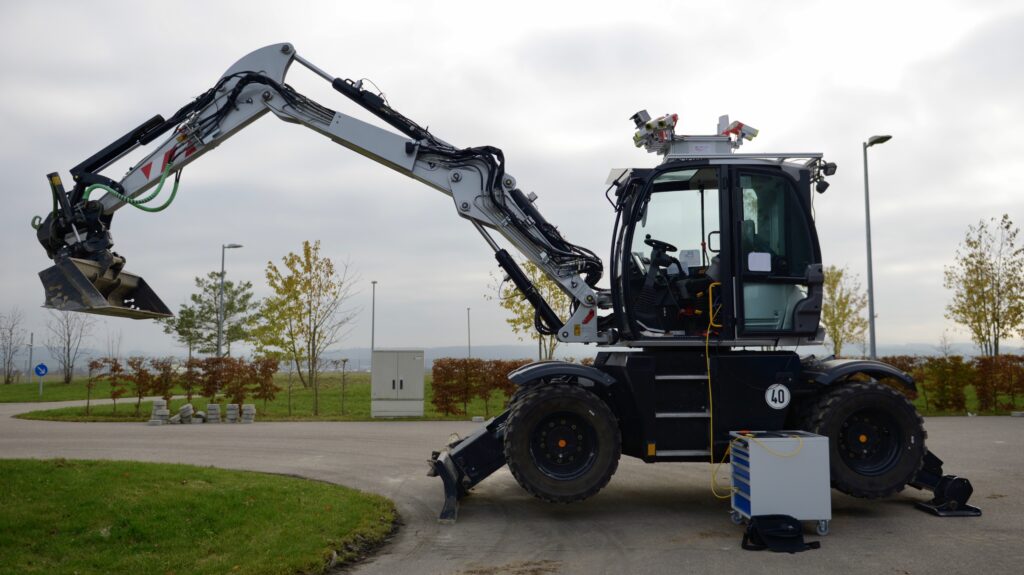
Real-time Model Predictive Control for Independent Metering Control Cylinders
Hydraulic cylinders are the most common type of hydraulic actuators. The control of their movement is performed by the joint control of the pump flow and the opening of a set of valves that directs it to the cylinder’s chambers. The so-called throttling action of the valves is one of the main sources of energy wastages on these machines, and a considerate actuation is key to an efficient operation.
In literature multiple approaches have been proposed for the control of hydraulic cylinders, all of them entailing the construction of a tailored controller for each machine configuration. This process requires an high development effort, and strongly relies on the experience of the engineer, resulting often in suboptimal performance.
An MPC approach is studied and evaluated also for this section of the system. Simulation assessments showed how a centralized optimal control of the pump and valves allows for a significant reduction of the energy consumption.
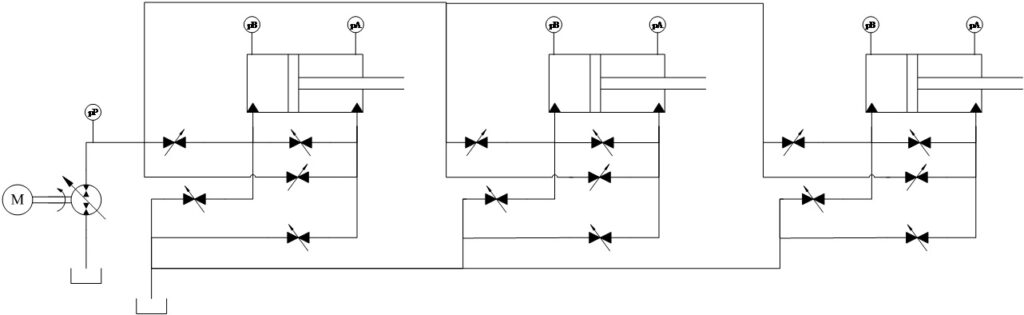